Testing management and optimisation
How to ensure the best performance and safety conditions for the start-up planning?
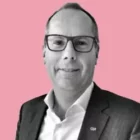
Bruno Pelé
Construction Management Operations Director
Graduate of the École Nationale Supérieure des Arts et Industries in Strasbourg, Bruno joined Assystem over 35 years ago as a test engineer. Involved in several major nuclear projects, he became responsible, in 2019, for the management of the construction and commissioning of Hinkley Point C in the United Kingdom. He is now in charge of these activities as part of the launch of the EPR2 programme in France.
How to ensure the best performance and safety conditions for the start-up planning?
The testing and commissioning phase is one of the key stages in the construction management of an industrial programme. Following the studies, design and construction phases of an infrastructure project, testing and commissioning represent the final milestone before the transfer of responsibility to the operator, under optimum operating and safety conditions.
Indeed, the commissioning of an installation requires that it has been tested, inspected and verified, to ensure that it complies with safety, performance and regulatory requirements: test strategy, preparation and performance of tests, and analysis of results are all solutions for anticipating deviations from specifications and safety requirements.
To optimise this key phase, digital testing platforms are now available, particularly for control systems, using simulation tools. These make it possible to increase efficiency, reduce commissioning costs and risks of regression, as well as ensuring skills upgrading for operating personnel.
Management and optimisation of testing: an essential step to deliver a functional, robust and safe installation…
The aim of industrial testing is twofold: firstly, to check and, if necessary, diagnose whether a plant or piece of equipment complies with the specifications; secondly, to simulate the performance of the facility in operation, in order to adjust its technical settings to guarantee optimum operation when it is commissioned. Once the tests have been performed, the next step is to ensure the smoothest possible transition from the end of construction to the transfer to the operator.
Implementing a testing methodology based on a functional approach for facilities is essential to guarantee quick and efficient commissioning. We need to make this switch as early as possible, from a market-based approach during the construction phase to a functional approach for testing. At Assystem, for example, our approach is based on anticipation, gradual start-up, and integration of the operator right from the end of construction, to ensure that commissioning is as smooth and rapid as possible.
Optimising an installation's start-up schedule therefore involves controlling testing in several key stages, where each component in the process has its own importance: mapping the installation geographically and functionally, validating with suppliers (especially control systems), taking the time and resources to ensure rigorous transmission of installations between assembly and testing, and finally providing support for gradual start-up from elementary functions to the main functions in order to identify functional failures and rectify them as quickly as possible..
Planning and running tests, evaluation of the results of the testing and commissioning phases, integration methods for the operator, test simulation (I&C platforms), anticipation of tests on suppliers' sites are the key success factors for delivering and maintaining a high-performance installation.
Assystem's teams applied this methodology when providing support for the construction and commissioning of the Olkiluoto EPR in Finland (OL3). Our experts provided project management services for the instrumentation and control of the plant's autonomous systems: validation of the supplier's technical documentation and of its test procedures (materials and instrumentation and control softwares), monitoring the manufacture of the cabins and the factory tests, carrying out the on-site acceptance tests, and finally producing the non-conformity test reports. This support throughout the testing phases has ensured optimum operating conditions for the commissioning of the EPR.
Risk management and safety from commissioning to decommissioning of the facility
During testing, it is important to validate compliance with the design requirements set out in the specifications, as well as those of the safety authorities, by demonstrating the conformity of all installations and activities with the applicable specifications.
Testing is a key part of nuclear safety and must be carried out by experienced personnel with solid expertise in order to avoid common mistakes. Preparing, coordinating, and supervising tests as well as analysing their results carefully are essential skills for reducing risks and preventing safety and security problems when the installation is put into operation.
The analysis phase of test results is one of the cornerstones in demonstrating the conformity of all systems. The use of powerful digital solutions, capable of aggregating considerable quantities of data and analysing them in relation to requirements, now complements the expertise of test engineers in evaluating any anomalies.
In the nuclear sector, safety issues are central, and the increasingly strict legislation is constantly adjusting to the context and to lessons learned. In the light of the Fukushima accident, for example, the French Nuclear Safety Authority (ASN) set out new technical requirements: one of which was to equip the entire French nuclear fleet with an 'ultimate' emergency power source. These ultimate emergency diesels are installed in 'bunkered' buildings within the power plants and are designed to resist all types of hazards (earthquake, flood, tornado, attack, etc.). Assystem's teams have made a direct contribution to the implementation of this new regulatory framework, taking charge of supervising the testing of all 56 ultimate units within the operating fleet:
In concrete terms, our tasks consisted of analysing Test Execution Procedures, drafting monitoring programmes, supervising assembly work, conducting test surveillance, analysing assembly and test non-compliance reports, assisting the customer's supervisors with endurance tests, managing and supervising the worksite and logistical activities relating to the tests.
The involvement of experts in testing and commissioning is therefore a prerequisite for the operational delivery and safe operation of complex installations. To optimise organisation, monitoring, quality, costs and timescales, engineering obviously relies on increasingly innovative solutions thanks to the use of digital technology.
Simulation solutions for test optimisation and control
On complex installations such as nuclear power plants, almost 100,000 electrical signals need to be tested, while guaranteeing the preparation, recording and control of all the data associated with the tests.
One of the possible solutions for digitalising testing and commissioning operations is the digital twin: as a model, it offers a concrete response to the challenges of agility, anticipation, safety and performance during the testing and start-up phases. The digital twin will enable tests to be optimised (i.e. reduced in number) by modelling the overall sequencing of tests and interfaces between elements using model-based systems engineering (MBSE), collecting and recording test and trial data on a real-time digital platform, and displaying data in real time using an artificial intelligence module that compares test results and suggests solutions in the event of deviations or non-compliance. The modelling coupled with the data collected in real time can also be useful for creating multiple scenarios which, through simulations, will make it possible to test different hypotheses and thus evaluate the behaviour of the installation during the test phases before commissioning.
As part of an EPR commissioning project, Assystem supported the development of a set of IT tools to digitise the testing and commissioning phases, particularly for I&C (Instrumentation & Control) systems. Our teams provided the customer with a dedicated digital solution capable of structuring the various test campaigns, managing test data (tests carried out, tests remaining, deviation reports), recording information shared within the teams in real time, as well as visualising and reporting on test progress using key progress indicators.
For the industry, the benefits of digitisation are obvious: time savings, efficiency and traceability, as digital technology makes it possible to present test data in the right format at the right time; improved access to data at any time and in any place on site; improved test performance and productivity for test engineers; and improved test security, thanks to the introduction of processes and procedures to prevent data loss.
Ensuring the delivery of a compliant, operational and safe installation, testing is therefore a strategic milestone in the life cycle of a complex installation and must be handled with the highest degree of rigour. The expertise and reliability provided by engineering and digital technology reinforce this guarantee from both a technical and functional point of view, and also ensure that testing is optimally integrated and coordinated with the other site phases, both upstream (design, construction, assembly) and downstream (transfer to operation and maintenance).