INDUSTRIAL TRANSFER: A STRAIGHTFORWARD MOVE OR RELOCATING A COMPLEX SYSTEM?
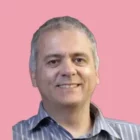
Jean-Pierre Pelle
Industrial transfers expert
An engineer by training, Jean-Pierre has more than 25 years of expertise in industrial transfers management. He is also Director of Assystem’s Innovation Department, allowing him to develop, among other things, specific solutions for industrial transfers.
The Covid-19 pandemic threw back into the spotlight the question of whether to repatriate certain strategic production capacity, especially in the pharmaceuticals and automotive industries. But whatever the scale of an industrial transfer, whether bringing back manufacturing capacity from overseas or simply moving within the same country (France for the purposes of this article), such an operation must be prepared months in advance and needs to factor in multiple constraints from a regulatory, logistical, and HR perspective that have to be analysed in every detail. To avoid falling into the traps that managing such a project can bring, we can now use systems engineering – with its methods for modelling complex systems – as well as artificial intelligence to leverage industrial data.
Industrial transfer, including in the context of a relocation, is not a simple move. The whole process requires anticipation, the analysis of risks , and the working our of different scenarios. Systems engineering can help with each of these all-important steps.
Whether it’s a move just miles down the road or a relocation from abroad, an industrial transfer needs to be thoroughly thought out. “Most of the time relocations are necessary due to production buildings being too old or located in urban areas where a lack of available land and high property prices make it impossible to extend or reorganize”, says our expert.
Relocation is back in the news at the moment. It’s being talked about not only by politicians campaigning for manufacturing capacity to be brought back to France but also by manufacturers themselves. The Covid-19 pandemic revealed the problems that delocalisation can cause and its impact on supply chains, which can be broken by stoppages – sometimes with no warning – of spart parts deliveries.
Although their numbers will never be massive, some manufacturers that are highly dependent on foreign suppliers – such as in the pharmaceutical and automotive industries – are asking themselves questions about where their strategic production capacity should be located and how reliable their supply chains are (for components, raw materials etc.). The same is true for companies seeking to set up more ethical and sustainable supply chains as part of their corporate responsibility initiatives. “Companies can no longer shirk their responsibilities in this domain as they face the reckoning of their employees, customers and investors”, adds our expert.
The decision-making process
Whatever the reason, and particularly since the Covid-19 pandemic, the decision to repatriate is never easy to take. Should I repatriate? Should I create a copy of the existing factory? What production is involved and in what conditions? Assystem can provide vital support in this area, helping its clients analyse the many factors involved (logistics, regulatory, HR, etc.) and the related risks before making a final decision.
“When we think about a factory, buildings and machines generally come to mind. But above all, a factory is the people who work in it and an accumulation of their combined skills and experience. When production capacity is repatriated, you need to rebuild that pool of expertise, which isn’t necessarily possible in France given that not all industrial trades are taught any more”, adds our expert, who believes that the human factor is one of the trickiest issues. WHen repatriating manufacturing facilities, political relations are another factor that unavoidably has to be taken into account.
The first step is to model production capacity by analysing all the interfaces that will change if the repatriation goes ahead. To deal with the complexity of this stage, we use systems engineering methods, such as MBSE (Model-Based Systems Engineering), moving from a traditional document-based approach to a model-based approach.
We redefine everything that’s necessary for production and perform a value analysis, criterion by criterion, and interface by interface
The whole of a factory’s ecosystem needs to be analysed, covering supplies, the downstream logistics chain, the impact of regulatory changes, human skills, the level of automation, standardisation when planning future policies for spare parts maintenance, quality controls, production costs and so on. “Modelling is also useful for later on in the process when it comes to actually organising the industrial transfer and, if required, for making a digital twin of the new factory.”, he explains.
Choosing the best relocation scenario
Once a decision to relocate has been made, the next question is how to continue operating so that client deliveries are not interrupted, given that most production is just-in-time nowadays.
How should this interim period be organised? Is it best to build up extra production before moving – which isn’t easy in a factory that’s going to be closed – or is it best to relocate as quickly as possible, running the risk of never being able to start up again? Or is it best to build a new factory and take the risk of deadlines and costs spiralling out of control?
By gaining a full understanding of the production ecosystem we can take everything into account before proposing different relocation scenarios based on our modelling
By carefully modelling a factory’s ecosystem we can propose different relocation scenarios and quickly assess the risks in terms of quality, costs and deadlines. There’s no one set way of doing things. Sometimes it’s best to relocate in one go (by stopping production, moving and starting up again at the new facility) or it’s possible to rebuild by completely duplicating a factory. But the most common and balanced way of doing things is to gradually relocate the machinery, with production continuing in parallel at both sites while creating temporary workflows. The impact of each of these scenarios can be simulated thanks to MBSE.
“Often when we’re choosing the relocation scenario, we can kill two birds with one stone by seeking a collective decision taken by all the players involved. That way we create a sort of “project spirit” from the outset and at the same time carry out an initial risk analysis which will be used as a roadmap for managing the project.”
Industrial data – the new challenge for industrial transfers
“A factory is obviously made up of buildings, machines and people, but it also includes data that is built up and stored over time.”
When we think of “industrial data” we think of instrumentation, inventory management and performance measurement. But that’s not all it is. Today, by analysing big data we can reconstitute certain know-how more quickly. “Ten years ago, if we relocated a biscuit factory, we had to rapidly recover the knowledge of the kneader (who adapted the amount of water used in the pastry depending on the weather conditions) and the technical expertise of the oven operator who regulated the temperature of the 150 burners every day. Getting this right in the new factory was a long and fastidious process.” This relationship between process and product is knowledge that’s often just in the heads of the people operating the machines. You have to rebuild that knowledge to get the new facility back up and running as soon as possible. And that’s exactly what artificial intelligence can help us to do.
The real challenge is being able to leverage industrial data very quickly, as well as managing other types of data. And once again, it’s all about experience and know-how!
Assystem meets this challenge by working with experts and operators to closely model the knowledge behind a factory’s production. Then, we combine this process with a data science approach by generating self-learning algorithms which are optimised by continuous data capture.
Managing the operational phase
“Managing an industrial transfer is like managing any other industrial project but often in half the time.”
Once the decision has been made to relocate it’s often the start of a race against time. Simply because it’s difficult to keep up the same output as at the old plant. Once the scenario has been chosen, an interim period begins when at the same time, we must prepare the destination site and prepare the transfer operations at the departure site. Some of the keys for success that we recommend are:
- Forming a project team with clearly defined responsibilities, in charge of the overall project.
- Using risk and interface management (a relocation means cutting off interfaces and re-establishing them).
- Putting in place intermediate milestones to guide all of the players involved.
- Using a shared management approach for planning and for the future settlement.
- Applying a relocation process that minimises change (is it really a good idea to “make the most” of the relocation to change processes?).
- Using relocation and inventory procedures that enable transferred assets to quickly return to their pre-move performance levels.
Another factor for success is efficiently managing all the data generated throughout the project. It’s important to make sure there is consistency between data related to planning, installation at the new site, inventories, relocation and production re-start procedures, truck packing, certification, asset management and of course industrial data concerning the factory’s assets. That’s why Assystem has developed a specific tool for effectively managing this interim period, which is essential for steering and overseeing all of the players involved in a relocation.
“The specific method we use at Assystem (modelling, risk analysis, scenarios, etc.) is combined with an on-the-ground approach and long-standing experience in managing complex and multi-sector infrastructure as well as digital technology”, concludes our expert, adding that each transfer project has its own specificities.