TRANSFERT INDUSTRIEL : DÉMÉNAGEMENT SIMPLE OU RELOCALISATION D’UN SYSTÈME COMPLEXE ?
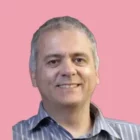
Jean-Pierre Pelle
Expert transferts industriels
Ingénieur de formation, Jean-Pierre a plus de 25 ans d’expertise dans la gestion des transferts industriels. Il est également Directeur du pôle Innovation ce qui lui a permis de développer, entre autres, des solutions spécifiques aux transferts industriels.
La pandémie due à la Covid-19 remet au cœur de l’actualité la question des relocalisations en France de certaines productions stratégiques, notamment dans les secteurs de la pharmacie ou de l’automobile. Mais, qu’il s’agisse d’un transfert industriel depuis l’étranger ou interne à l’Hexagone, une telle opération doit se préparer des mois à l’avance et tenir compte des multiples contraintes réglementaires, logistiques, humaines… qu’il faut analyser dans le détail. L’ingénierie système, de par ses méthodologies de modélisation des systèmes complexes, et l’intelligence artificielle, de par son exploitation des données industrielles, permet aujourd’hui d’anticiper les pièges dans la gestion des transferts de production.
Letransfert industriel, y compris dans le cadre d’une relocalisation, n’est pas un simple déménagement. Il nécessite anticipation, analyse de risques et élaboration de différents scénarios… Des étapes incontournables durant lesquelles l’ingénierie système peut aider à la gestion de projet.
Qu’il s’agisse d’un déplacement de quelques kilomètres de distance ou d’une relocalisation en France depuis l’étranger, un transfert industriel doit être une opération longuement réfléchie. « La plupart du temps, il s’impose du fait de la vétusté des bâtiments de production, ou encore lorsqu’il s’agit d’une implantation située en zone urbaine où la raréfaction et le prix du foncier excluent toute possibilité d’extension ou de réorganisation », explique d’entrée l’expert.
Les relocalisations sont de nouveau un sujet d’actualité, souvent évoquées par les politiques qui militent pour une réindustrialisation de l’Hexagone, mais également par les industriels eux-mêmes. La crise sanitaire de la Covid-19 a en effet montré les limites des délocalisations et leur impact sur les approvisionnements provoquant des ruptures de flux de par l’arrêt brutal parfois de la livraison de pièces détachées.
Aussi, même si ce ne sera jamais un mouvement massif, certains industriels, très dépendants de fournisseurs étrangers comme dans la pharmacie ou l’automobile, se posent aujourd’hui la question de l’implantation de leurs productions stratégiques et de la fiabilité de leurs chaînes d’approvisionnement (composants, matières premières…). Ces réflexions rejoignent celles de la mise en place de chaînes logistiques plus éthiques et durables, dans le cadre d’initiatives environnementales et sociales. « Face à leurs salariés, leurs clients et leurs investisseurs, ils ne peuvent plus se dédouaner de leurs responsabilités à ce sujet », constate l’expert.
La prise de décision
Quelle qu’en soit la raison, et d’autant plus depuis la pandémie de Covid-19, la décision d’une relocalisation n’est jamais simple à arrêter. Est-ce que je relocalise ? Est-ce que je duplique l’usine ? Quelles productions sont concernées et dans quelles conditions ? D’où l’importance pour Assystem d’accompagner ses clients dans l’analyse des multiples paramètres (logistiques, réglementaires, humains…) et des risques pour aboutir à la décision finale.
« Lorsque l’on visualise une usine, on a surtout en tête des murs et des machines. Mais une usine, c’est avant tout des femmes et des hommes, des compétences et de l’expérience accumulée. Lorsque l’on rapatrie une production, il faut reconstituer ce savoir, que l’on ne retrouve pas obligatoirement en France, pays où l’on ne forme plus à tous les métiers industriels », rappelle l’expert, qui estime que la question du facteur humain est l’une des plus difficiles à résoudre. C’est pourquoi, dans le cadre des relocalisations surtout, le lien avec le politique par exemple est incontournable.
La première étape consiste donc à modéliser la production en analysant l’ensemble des interfaces qui seront modifiées dans une potentielle relocalisation. Face à cette complexité, on utilise alors des méthodologies d’ingénierie système, comme le MBSE (ou Model Based System Engineering) visant à passer d’une approche classique documentaire, textuelle, à une approche modèle.
On redéfinit tout ce qui est nécessaire pour produire et on en fait de l’analyse de la valeur critère par critère, interface par interface
Les approvisionnements, la chaîne logistique aval, l’impact du changement de réglementation, le facteur humain, le niveau d’automatisation, la standardisation pour anticiper la politique de maintenance en termes de pièces détachées, les contrôles qualité, les coûts de production…, l’ensemble de l’écosystème doit être analysé. « Cette modélisation sera également utile par la suite pour l’organisation du transfert et, si besoin, pour la réalisation d’un jumeau numérique de la future usine », précise-t-il.
Le choix du scénario de transfert
Une fois la décision prise, se pose alors la problématique de la continuité d’activité synonyme de non-rupture de livraisons pour les clients pour des productions réalisées pour la plupart du temps en flux tendus.
Comment organiser cette période transitoire ? Doit-on privilégier des avances de production difficile à réaliser dans une usine qui va perdre son activité, doit-on transférer au plus vite au risque de ne jamais pouvoir redémarrer, doit-on construire une nouvelle usine au risque de voir les délais et les coûts s’envoler ?
Comprendre parfaitement l’écosystème de production permet de tout prendre en compte avant de proposer différents scénarios de transfert à partir de la modélisation
Bien modéliser l’écosystème permet de proposer différents scénarios de transfert et d’évaluer rapidement les risques sur la qualité, les coûts et les délais. Il n’y a pas une règle applicable à tous. On peut transférer en une seule fois (on arrête l’usine, on la déménage et on redémarre), on peut reconstruire en dupliquant intégralement l’usine, on peut aussi choisir le scénario le plus répandu et le plus équilibré en transférant petit à petit les équipements et en produisant en parallèle sur les deux sites tout en créant des flux provisoires. La simulation associée à la modélisation MBSE mesurera l’impact de chacun de ces scénarios.
« Bien souvent, lors du choix du scénario, on fait d’une pierre deux coups en recherchant une décision collégiale avec l’ensemble des acteurs : on crée d’emblée « l’esprit projet » et on effectue en même temps la première analyse de risque qui servira de fil directeur à la gestion du projet ».
Les données industrielles, nouvel enjeu des transferts industriels
« Une usine, ce sont bien sûr des murs, des machines, des femmes et des hommes… mais aussi des données accumulées et stockées au cours du temps ».
Lorsque l’on pense « données industrielles », on pense instrumentation, gestion de stocks, mesure de performances. Mais ce n’est pas tout. L’analyse des données de masse (big data) permet aujourd’hui de reconstituer plus rapidement certains savoir-faire. « Il y a une dizaine d’année, en transférant une usine de production de gâteaux secs, il fallait retrouver rapidement le savoir-faire du pétrisseur (qui ajoutait plus ou moins d’eau à la pâte en fonction de la météo) et du cuiseur qui réglait quotidiennement les 150 brûleurs du four. La mise au point a été longue et fastidieuse dans la nouvelle usine ». Cette connaissance intime du rapport entre process et produit se trouve bien souvent seulement dans la tête des opérateurs. Il faut pouvoir la reconstituer pour aller au plus vite dans le redémarrage du nouveau site et l’intelligence artificielle peut le permettre.
Le vrai enjeu est d’exploiter les données industrielles très rapidement, mais aussi de gérer d’autres types de données. Et là, on en revient à l’expérience et au savoir-faire !
Le parti-pris d’Assystem est de modéliser au mieux avec les experts et les opérateurs le savoir-faire lié à la production et de coupler celui-ci avec une démarche de data-science en générant des algorithmes auto-apprenants optimisés par une captation de données en continu.
La gestion de la phase opérationnelle
« Gérer un transfert industriel, c’est gérer une projet industriel classique mais en devant aller parfois deux fois plus vite ».
Une fois la décision prise de transférer, c’est souvent une course contre la montre qui s’engage. En effet, il est alors difficile de maintenir les mêmes exigences de production sur le site de départ. Une fois le scénario choisi, une période transitoire s’ouvre alors pendant laquelle on doit en même temps préparer le site receveur et préparer sur le site de départ les opérations de transfert. Les clefs de réussite que nous recommandons s’appuient entre autres sur :
- Une équipe projet clairement identifiée et pilotant l’ensemble du projet
- Une gestion par le risque et par interface (transférer, c’est couper des interfaces et les rétablir)
- Des jalons intermédiaires permettant une meilleure implication de tous les acteurs
- Une gestion mutualisée du planning et de l’implantation future
- Un process de transfert minimisant les modifications (est-ce vraiment une bonne idée de « profiter » du transfert pour modifier le process)
- Des procédures de transfert et d’état des lieux permettant de retrouver rapidement les performances des moyens déplacés.
Une des clefs de la réussite réside dans la gestion de l’ensemble des données générées tout au long du projet. On doit assurer la cohérence entre les données d’implantation, de planning, d’états des lieux, de procédures de transfert et de remise en production, de colisage de camion, de certification, de gestion de patrimoine avec bien entendu les données industrielles liées aux moyens. C’est pourquoi Assystem a développé un outil spécifique pour gérer au mieux cette période transitoire. C’est un prérequis indispensable pour piloter l’ensemble des acteurs concernés par le transfert.
« La méthode spécifique d’Assystem (modélisation, analyse de risques, scénarios…), se couple ainsi avec une approche terrain, une longue expérience dans la gestion d’infrastructures complexes et multisectorielles, et le digital », conclut l’expert, conscient que chaque projet de transfert contient ses spécificités propres.